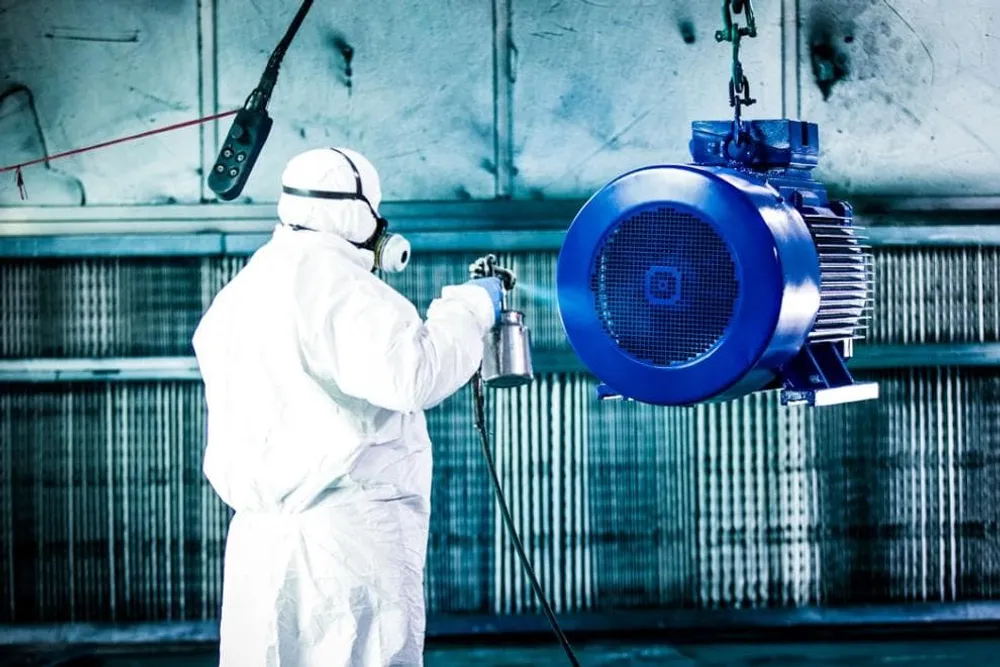
A Fabbrico, nella Bassa Reggiana, a pochi chilometri da dove è nato il cantante Ligabue, dal 1884 si producono trattori. Siamo nel cuore della “Motor valley” emiliana, e nel pieno centro della cittadina ha sede la Argo Tractors. Fino al 2011, le trasmissioni dei McCormick, marchio di punta del gruppo controllato dalla famiglia Morra , venivano prodotte in Francia e i trattori assemblati in Gran Bretagna. Ora, invece, si fa tutto in Italia. Il settore ha sofferto assai la crisi cominciata nel 2008, ma da allora il gruppo è passato da 1.600 a 1.650 dipendenti, e il fatturato, che nel 2010 era stato di 430 milioni di euro, quest’anno non è lontano da quota 500 milioni, per l’85 per cento realizzato con l’export. «Qui esistono le competenze, la passione, le scuole tecniche giuste. E aver concentrato in zona l’intera produzione è motivo di grande soddisfazione per tutti noi dipendenti», racconta Antonio Salvaterra, il capo del marketing, che nel giro di ricognizione in fabbrica spiega: «Vede queste linee di assemblaggio? Sono state recentemente ammodernate in chiave Kaizen, per adeguarsi al sistema della “produzione snella”. E qui, dove poche settimane fa c’era un terreno inutilizzato, l’area spedizioni ha raddoppiato la superficie», dice mentre suona la sirena della pausa pranzo.
VIDEOMAPPA: ECCO LE SEI AZIENDE CHE TORNANO IN PATRIA
RUGGISCE IL TOSAERBA
Un paio d’ore al volante verso Nord ed ecco la zona industriale di Castelfranco Veneto, la città del Giorgione, in provincia di Treviso. Uffici e capannoni della GPP - Global Garden Products - sono circondati da prati curati come campi da golf. Ovvio, siamo nel quartier generale del leader europeo dei tosaerba, un fatturato di 450 milioni di euro e 500 addetti che diventano 800 nei picchi stagionali. Meno scontata la marcia indietro inserita di recente dal gruppo veneto che, tra il 2005 e 2008, aveva aperto stabilimenti in Slovacchia e Cina, mantenendo solo parte della produzione in Italia e contando su una gamba svedese, dopo l’acquisizione dei tosaerba Stiga. «Negli ultimi mesi abbiamo concentrato tutte le funzioni più importanti qui a Castelfranco, riportando in Italia l’alto di gamma, che prima era assemblato in Svezia, e assumendo una trentina di ingegneri e tecnici», racconta Massimo Bottacin, capo delle risorse umane. Uno dei nuovi è Varna Vallone, ingegnere, l’unica donna del team di ricerca e sviluppo in cui lavora. «Mi sono laureata a Udine, ho 26 anni e sono felice di essere qui perché nel trevigiano non ci sono tante imprese che puntano sulla ricerca, mandando i giovani come me a formarsi con i migliori esperti d’Europa», racconta con la voce rotta dall’emozione, maneggiando un sofisticato strumento di rilevazione. Sono già centinaia i nuovi posti di lavoro creati e quelli vecchi salvati dalle operazioni di rimpatrio avvenute o in divenire nella più classica manifattura industriale. Secondo un pool di docenti di diverse università, guidato da Luciano Fratocchi, il reshoring avrebbe coinvolto una novantina di aziende, anche se in alcuni casi per ora si tratta di promesse.
PIÙ RAPIDI DEI CINESI
Del resto neppure negli Stati Uniti, dove dell’auspicata tendenza si parla da tempo, i numeri sono clamorosi. «I più citati dati sul back-shoring arrivano da un sondaggio con 300 amministratori delegati di aziende, che talvolta hanno dato per realizzata quella che era solo un’idea», dice Francesco Stefanelli, ricercatore che ha studiato il tema al Mit di Boston. Negli Usa, le imprese che sono tornate o intendono farlo sono stimolate da una burocrazia light, ma soprattutto da un costo dell’energia che è calato nettamente, regalando un grande vantaggio competitivo. Condizioni che in Italia non si sono verificate: chi è rientrato o vuol farlo, sia nella meccanica sia nella moda, lo fa spinto dall’accoppiata velocità-qualità. Il Made in Italy piace perché è sinonimo di pregio, nell’abbigliamento come nella meccanica, e il cliente ha sempre più fretta. I tempi di trasporto dal Far East non sono più compatibili con questa accelerazione e i tecnici bravi, così come gli artigiani esperti nel trattare cuoio o tessuti di pregio, stanno in Italia. Quindi si rimpatriano soprattutto le produzioni più costose e complicate.
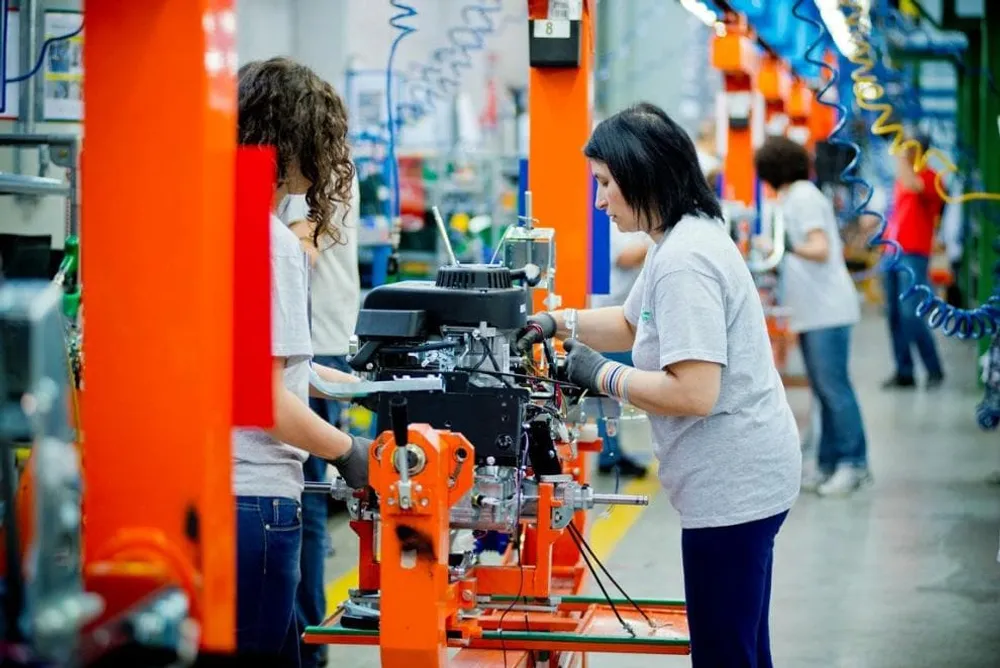
Se Svezia, Gran Bretagna e Francia non sono Paesi dove la manodopera è economica, la Repubblica Ceca è uno di quei posti dove finora si delocalizzava per risparmiare sulle paghe. Ora, i costi si possono comprimere anche in Abruzzo. Lo stabilimento della Fiamm, leader europeo delle batterie per auto, è alla periferia di Avezzano, 40 mila abitanti circondati dai monti della Marsica. Quando si entra nel reparto fusioni l’odore di piombo pervade le narici. Gli operai lavorano su tre turni, 24 ore al giorno, una rarità nell’Italia attuale. La Fiamm, che realizza all’estero il 70 per cento dei suoi 550 milioni di fatturato, fino a cinque anni fa aveva una fabbrica in Boemia, a fianco allo storico impianto della Skoda. Ora, ad Avezzano, ci sono 140 dipendenti in più rispetto ad allora. E l’impianto di Mladá Boleslav ha chiuso. Quando deve spiegare i motivi della scelta controcorrente, Stefano Dolcetta, titolare del gruppo oltre che vice presidente di Confindustria, precisa che è stata fatta in virtù di situazioni particolari. «L’impianto abruzzese era in disuso, stavamo per chiuderlo. Al contempo anche nella Repubblica Ceca avevamo problemi: la fabbrica era poco produttiva e i nostri operai erano attirati dalla vicinissima Skoda, per cui per trattenerli dovevamo alzare le paghe». Ecco l’idea: contrattare con i sindacati una riduzione dei salari, in cambio di un investimento da 30 milioni di euro per rifare lo stabilimento. In soldoni, il costo medio per un operaio è sceso da 24 a 18 euro. «La manodopera, ad Avezzano, resta comunque più cara di quasi tre volte rispetto a Mladá Boleslav», precisa Dolcetta, «ma questa differenza è compensata dalla maggiore produttività e dalla riduzione degli scarti».
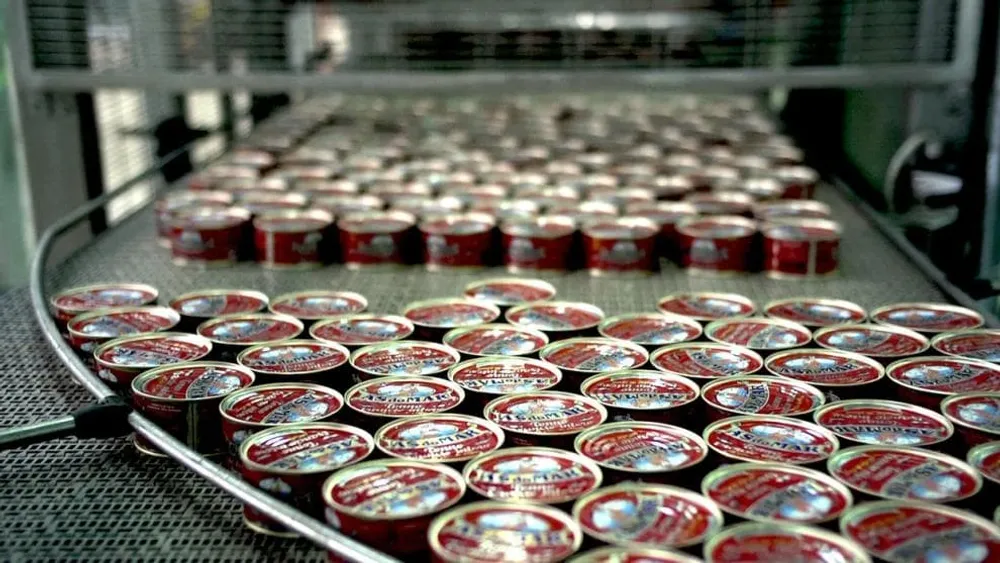
PINNA GIALLA PARLA SARDO
A Olbia, in Sardegna, gli scarti si riutilizzano. «Li trasformiamo in cibo per gatti», spiega Giovanni Placido, direttore dello stabilimento sardo della Asdomar, indicando un nastro che trasporta piccoli pezzi di tonno dentro un cassone. Vito Gulli, azionista di maggioranza del gruppo Generale Conserve, che controlla anche marchi come Manzotin e De Rica, quando ha scelto di puntare sull’Italia invece che sul Portogallo sapeva che non avrebbe risparmiato sulla manodopera. «Un operaio lì costa 5,5 euro l’ora, quasi un quarto rispetto a qui», dice, «ma personalmente credo in un’altra strada: il consumatore premierà sempre più chi dà lavoro agli italiani. La crisi della nostra economia è stata gran parte causata proprio dalla delocalizzazione. E tanti altri imprenditori seguiranno il nostro esempio». Che cosa ha fatto, Gulli? Ottenuto il controllo di Asdomar, ha deciso di spostare la lavorazione del tonno a pinna gialla dalle Azzorre, in Portogallo, a Olbia. Dove nel frattempo era stata chiusa la fabbrica del Tonno Palmera. Dopo averne rilevato i macchinari, Gulli ha costruito uno stabilimento nuovo di zecca, assumendo i 200 lavoratori che la Palmera aveva lasciato a spasso. È per questo che oggi, a ridosso delle spiagge della Costa Smeralda, tre uomini in tuta blu e caschetto rosso scaricano da un camion decine di tonni congelati. Pescioni da 50 chili l’uno. Pronti per essere tagliati, cotti e inscatolati. «Una svolta costosa, 25 milioni di euro investiti, ma non romantica: il tonno Made in Italy», dice Gulli, «è apprezzato e i clienti sono disposti a pagarlo un poco di più. Lo dimostrano le nostre vendite, che aumentano del 5-10 per cento all’anno. E intanto, siamo arrivati a trecento dipendenti».
ORGOGLIO MONTANARO
A essere pignoli, quello fatto da Gulli è più un salvataggio industriale che un reshoring, visto che lui la produzione all’estero non l’aveva trasferita. L’esempio della trevigiana Aku, invece, è da manuale: l’azienda, che produce scarponi da montagna, come altre in Veneto aveva delocalizzato in grande stile, trasferendo il 90 per cento della produzione da Montebelluna a Cluj, in Romania. Tre anni fa il cambio di rotta: ha rimpatriato alcune linee e ora realizza a Montebelluna il 30 per cento dei suoi scarponi. «Un operaio in Romania costa ancora il 40 per cento in meno rispetto all’Italia», racconta il titolare, Paolo Bordin, «ma nel nostro settore, che è di nicchia, non si può guardare solo alla convenienza: dobbiamo lavorare sulla qualità, e questo lo possiamo fare meglio da noi».
QUANT'E' CARO IL DIPENDENTE
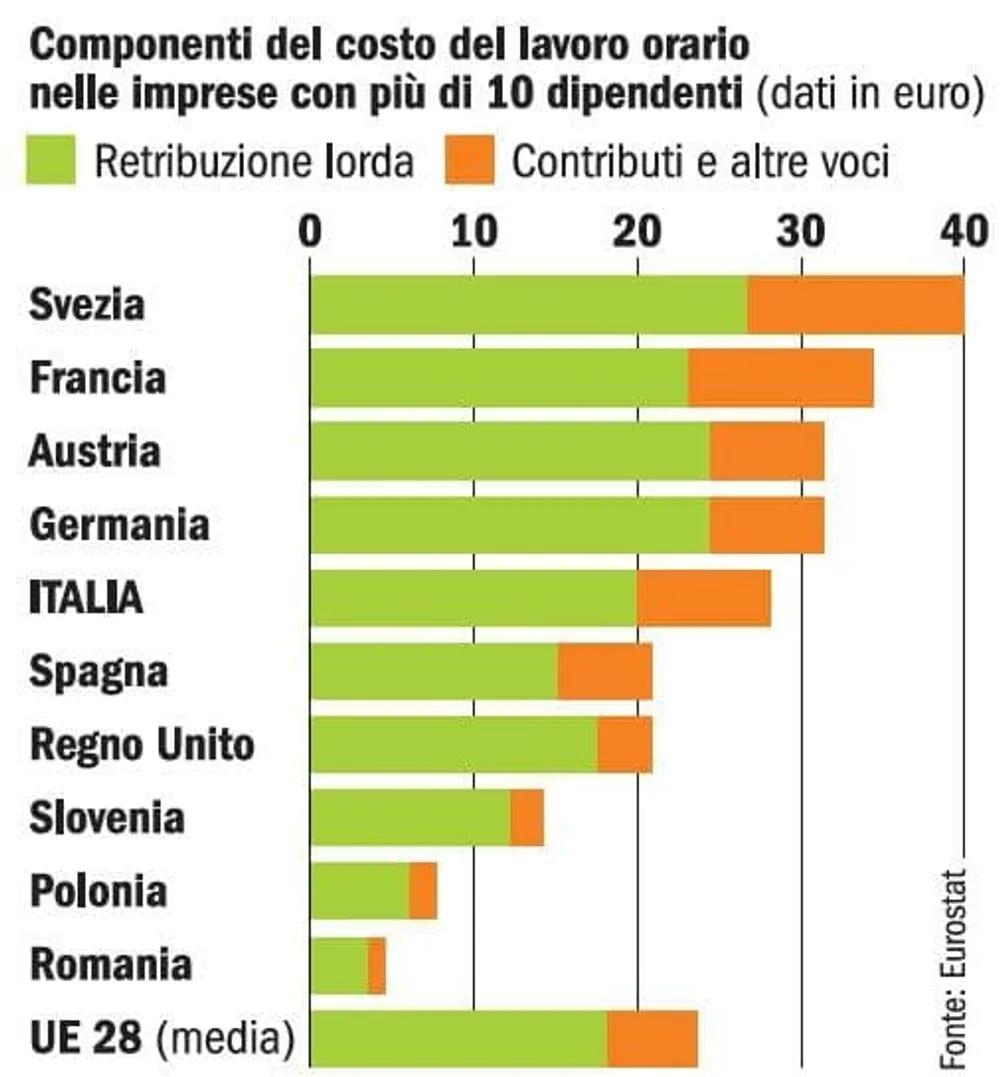
Anche nell’indotto auto, assicura Massimo Carboniero, contitolare della vicentina Omera - un centinaio di addetti, 20 milioni di ricavi e ordini in crescita pure per il 2015 - si muove qualcosa: «Non posso fare nomi ma negli ultimi 12 mesi alcuni clienti italiani hanno ripreso a ordinare le nostre presse per star dietro alle richieste di case automobilistiche europee, anche in Germania e Spagna», dice Carboniero, che è vicepresidente dell’Ucimu, l’associazione dei produttori di macchine utensili. Le nuove commesse sono arrivate perché, per certe lavorazioni, gli europei, e gli italiani soprattutto, raggiungono una qualità che altrove non c’è. «In qualche caso i fornitori italiani dei gruppi automobilistici hanno incrementato i dipendenti», aggiunge l’industriale veneto. Che il settore evidenzi segnali di risveglio lo confermano i numeri: la componentistica automotive italiana (2.400 aziende), nei primi sei mesi del 2014 ha esportato prodotti per 10,2 miliardi, il 5 per cento in più dell’anno scorso.
COME CORRE LA POLONIA
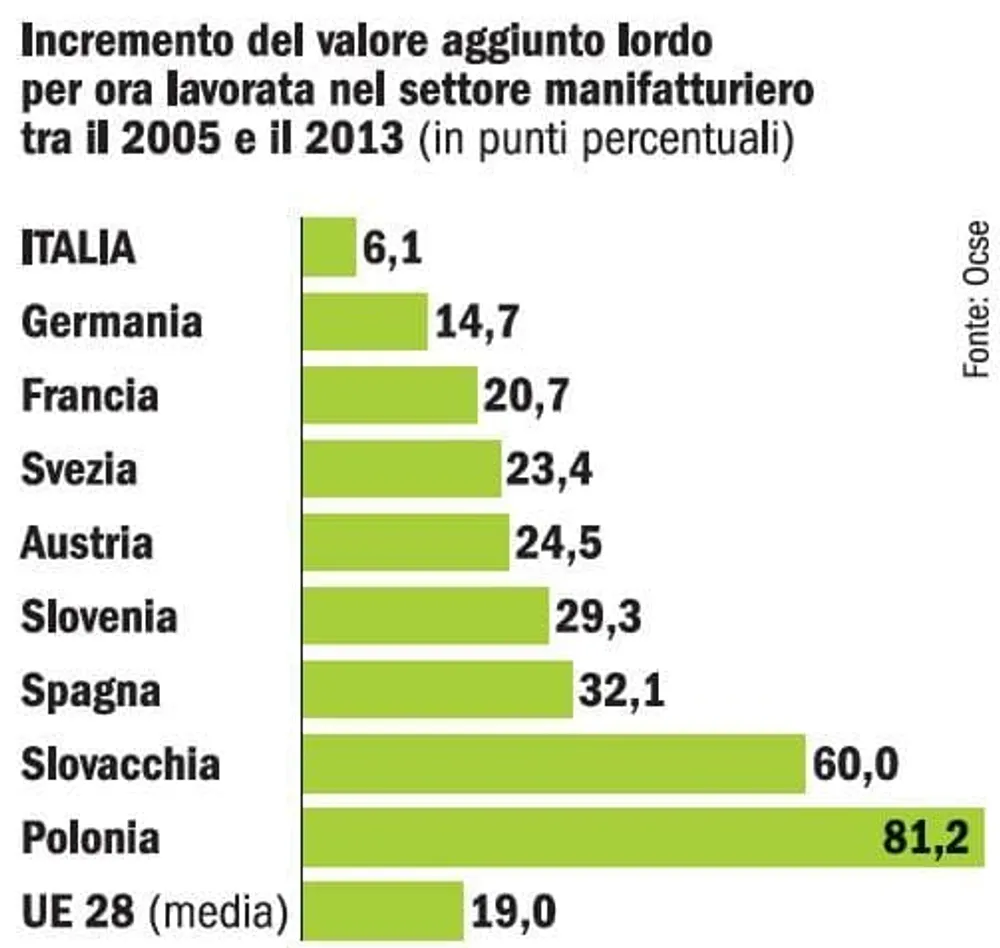
Corre invece su due ruote, l’operazione-rientro della bolognese Wayel. È la scommessa di Giorgio Giatti, che una trentina d’anni fa ha iniziato importando condizionatori Mitsubishi e ora fattura 40 milioni di euro. Fino a l’estate scorsa Wayel importava dalla Cina bici a pedalata assistita e motorini elettrici. Oggi, in un laboratorio di Borgo Panigale, a pochi metri dalla sede delle moto Ducati, quei mezzi sono montati da una manciata di operai appena assunti: quattro, ai quali si aggiungono tre giovani piazzati negli altrettanti negozi aperti a Milano, Firenze e Bologna. Poca cosa, al momento. Per vedere il futuro bisogna andare dall’altra parte di Bologna, vicino al nuovo grattacielo Unipol. Due ruspe gialle aspettano la fine del temporale per ricominciare a spianare il terreno. È qui che a fine 2015 sorgerà lo stabilimento: 12 milioni investiti, 35 mila pezzi all’anno tra motorini e bici elettriche. E 39 posti di lavoro. «Il mercato ha grandi prospettive, soprattutto nel Nord Europa, e i concorrenti sono pochi», dice Giatti. Perché produrre a Bologna invece che a Shanghai? «Per vendere in quei mercati ci vuole la qualità del Made in Italy. E poi la Cina non è più quella di prima: gli stipendi degli operai crescono del 20 per cento l’anno e la moneta si sta rivalutando. I costi della manodopera restano più bassi dei nostri, ma con i risparmi logistici e la maggiore automazione contiamo di compensare il differenziale».
MOTORE LOMBARDO
Di qualità e Cina parla volentieri anche Matteo Colombo, uno dei titolari del gruppo Felm. Il suo quartier generale sta all’estremità della zona industriale di Inveruno, in provincia di Milano, non distante da Malpensa. Fondata dal nonno Michele, la Felm è specializzata in motori elettrici. È stata tra le prime a puntare sulla produzione in Cina, nel lontano 1984. E pure tra le prime, però, a innestare - parzialmente - la retromarcia. La parte più redditizia dell’attività, per la società milanese, è la personalizzazione di motori speciali, ad alta potenza, destinati agli impieghi più vari: dagli acquedotti alle navi da crociera. «Un business che richiede progettazione personalizzata, tecnici che la sanno lunga e una maniacale attenzione al controllo della qualità», dice Alessandro Alberti, capo della produzione, mentre guarda quasi con affetto una macchina speciale messa a punto per un grande ventilatore, e prova a spiegare quanto sia importante il ruolo della cosiddetta “avvolgeria” (il filo di rame avvolto sul lamierino magnetico è il fulcro dei motori elettrici). Dall’azienda escono manufatti da 150 euro, standard, ma vengono messi a punto pure bestioni che possono costare oltre 100 mila euro. E che non devono avere problemi: «Anche se, per ogni evenienza, siamo pronti a salire su un aereo persino il venerdì pomeriggio, se un cliente ha bisogno di noi». Alla Felm lavorano in 35, di cui nove tecnici e ingegneri. Se le cose continueranno ad andar bene (il fatturato quest’anno si aggira intorno ai 20 milioni di euro), nei prossimi mesi qualche assunzione potrebbe scapparci, lascia intendere il titolare.
E la moda, simbolo del Made in Italy? I graditi ritorni coinvolgono vestiti, scarpe, accessori e gli annunci fioccano, anche se, per ora, la ricaduta occupazionale sembra modesta. Sergio Tegon, patron della veneziana Seventy - pantaloni, camicie, giacche - ha detto di aver riportato una bella fetta della produzione in Italia, affidandola a fornitori che, ha dichiarato in un’intervista a un giornale locale, «hanno revisionato le vecchie macchine spente per la delocalizzazioni e le hanno rimesse in moto». Un altro veneto, Alberto Baban (che è anche il presidente dei “piccoli” di Confindustria), insieme ad altri soci - tra cui l’ex amministratore dell’Eni, Paolo Scaroni - ha rilevato la Gta Moda, che da mezzo secolo sforna pantaloni classici e sportivi, promettendo che la produzione rientrerà in Italia dalla Romania. Alla Gaudì di Carpi, nel modenese, dicono invece di aver riportato in Italia dalla Cina, già un paio di anni fa, «alcune produzioni di prima fascia, ora realizzate tra l’Emilia e la Toscana». L’attività è stata affidata a due laboratori esterni che, ironia della sorte, appartengono ad artigiani cinesi.